静電気除電の品質改善対策
静電気トラブルを改善する場合、QCサークル等でよく使用されている下記のステップで改善を進めます。
問題の認識⇒現状把握⇒原因分析⇒対策立案、実施⇒効果確認⇒歯止め&標準化
現状把握:
『品質管理』は正しい測定から始まります。
静電気トラブルを改善する為に初めに現状把握を客観的データーに基づいて把握してください。
それにはまず、静電気測定器にて現場の帯電量を測定して下さい。
目に見えない静電気も静電気測定器で測定し、数値化すれば「静電気の見える化」が可能です。
グラフ等で表現すれば改善前との差も誰が見てもわかるようになります。
また、現在の歩留り率、チョコ停止率等のデーター収集も重要です。
静電気測定器の選び方
半導体工場では数Vで半導体が破壊されてしますので帯電量を測定する電位計も精度が高く、信頼性の高い製品が必要ですが価格が10万円以上と高額です。
一方、食品工場での静電気によるトラブルは数百Vから発生するトラブルが多いので
測定精度は少し低いが価格が安価な2万円前後の静電気測定器でも使用できます。
工場の必要とする要求レベルに適した静電気測定器を選択してください。

静電気測定器
原因分析
収集した客観的データーをそのままの数値ではわかりにくいので品質管理の基礎のツールである『QCの七つ道具』(特性要因図、パレート図、ヒストグラム、グラフ、管理図、チェックシート、散布図、層別)を活用して原因分析を行います。
具体的な事例として静電気発生の特性要因図を下記に記載しました。
特性要因図 事例
問題点に対してその原因を全員で提起し視覚的にまとめ、重要と思われる要因について的を絞って効果的に改善を推進していくための手法が特性要因図です。
特性が起きる要因として考えられる大きな要因(5M+1E)を上げそれを大骨として矢印で記入し、次に中骨、小骨を記入します。
*5M+1EとはMan(人) ,Machine(設備), Material(材料), Method(方法), measurement(測定)、 Environment(環境)の事。
トラブル事例内容:
『A食品工場では最近、自動プラ袋供給機トラブルによるチョコ停止が増加していた、要因を絞り込んだ結果、設備異常が発生した要因がプラ袋の帯電除去用に使用している除電器の放電針の汚れによる除電不足だった』
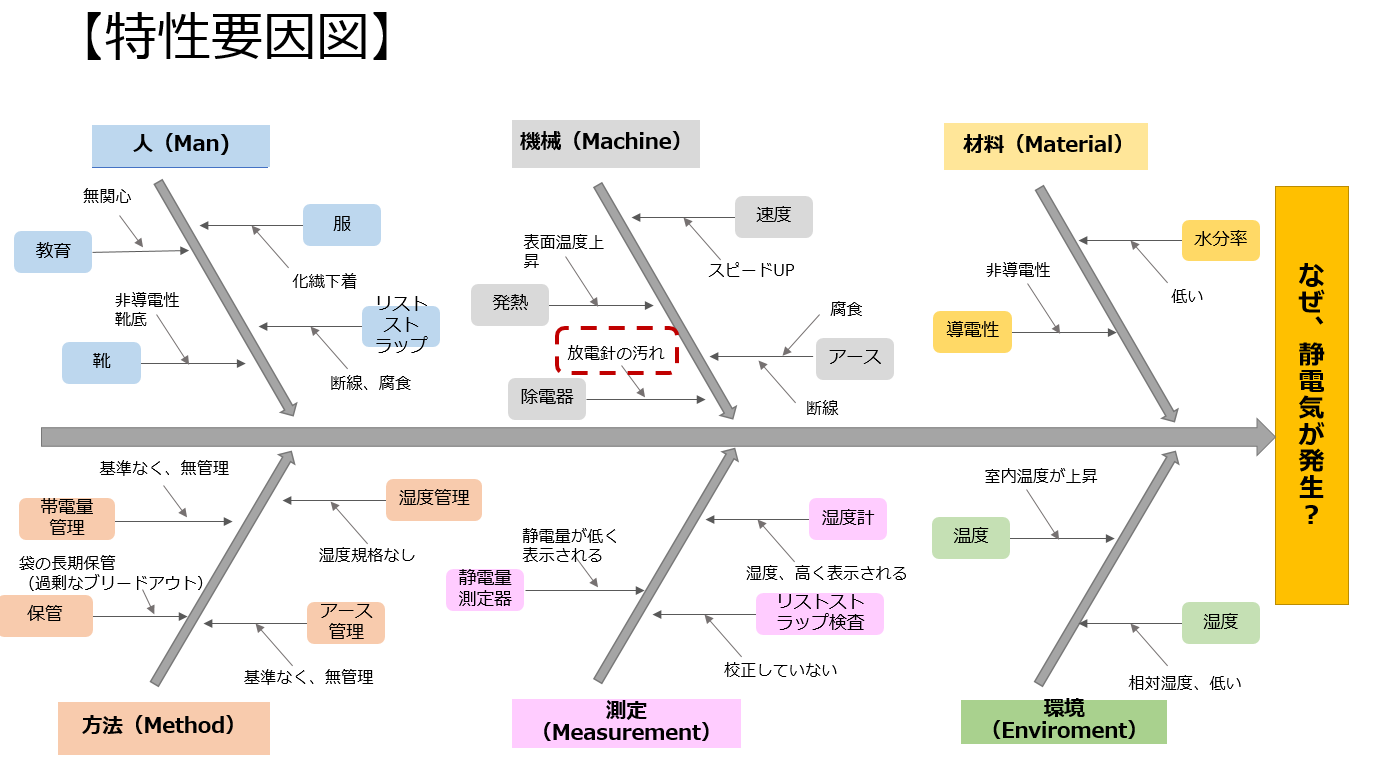
特性要因図
「なぜなぜ分析」事例
次に対策を検討するためになぜなぜ分析を実施しました。
不良や不具合など問題の真因を追求する手法に「なぜなぜ分析」があります。なぜなぜ分析は、一つの現象に対してなぜそれが発生するのかを自答自問することで、現象を発生させている真因を思いつきで考えるのではなく、規則的に順序良く漏れなく出し切る為の方法です。 なぜなぜ分析を効率的に進めるには、5W1Hの改善検討の原則を適用し、発生系のなぜ?と流失系のなぜ?を追究し、真の原因を突き詰めて対策を作成、実施します。
(5W1Hとは5つのW(what、where、 when、 who、why)と1つのH(how)の事です。)
事例では最終的に発生系の対策『放電針の定期清掃』及び流失系の対策『除電器の定期検査』迄、問題を追究します。
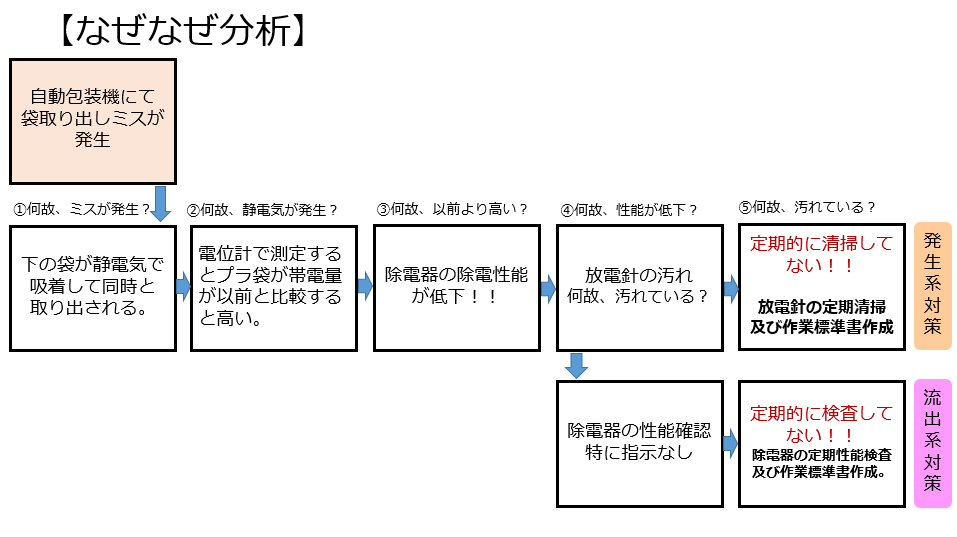
なぜなぜ分析
対策&立案:
静電気トラブルの真の原因がわかったら、その対策を考えて、実行します。
その際には次の二つの対策を検討します。
①静電気トラブル発生対策:
静電気トラブル発生の真の要因に対する対策。
事例の場合は放電針の定期清掃
静電トラブル流出系対策:
流出、検査ミスした要因に対する対策
事例の場合は除電器の定期性能検査。
効果確認:
放電針を清掃する前後のプラ袋の帯電量を測定し、比較します。

効果
歯止めと標準化:
静電気トラブル対策に効果があれば、その対策を継続させる為に作業標準書を作成
して、誰でもが実施できるように教育します。
以上が静電気トラブル発生時の基本的な品質改善の進め方です。
*静電気除電については別サイトに詳細記事を記載してありますので参考願います。